Introduction - N9XG
We're building an RV9A together. The tail number is already reserved and is "N9XG"
It's the biggest project either of us has ever started. We're having a lot of fun and learning many things about airplane construction and about ourselves as well. This site is about the process, and our progress.
We will be updating this from time to time with progress reports. If you can't see enough detail in any of the pictures you can click on them and they will expand (like Magic).
It's the biggest project either of us has ever started. We're having a lot of fun and learning many things about airplane construction and about ourselves as well. This site is about the process, and our progress.
We will be updating this from time to time with progress reports. If you can't see enough detail in any of the pictures you can click on them and they will expand (like Magic).
Friday, June 29, 2012
It's shocking how out of date I've let this become. We were at the point where we were considering giving up on the project. Then a friend came by and sparked the dream again. He said, "You have to do this! If you don't, it will haunt you." So we decided to enlist the assistance of Synergy in Eugene. Wally Anderson (the owner of Synergy) said he thought we could finish it up in a few weeks with their help. So June 13th Bob and I drove the whole project down to Eugene. Wally tells us that it will go faster than he thought, because "you've already done all the hard stuff". We will be working on it thru August and expect to have it finished by September.
Saturday, June 19, 2010
Back in the air
I got fed up with this not flying thing. So I went in and hired a CFI to help me make sure I'm still safe. We did about 1.5 hours on the ground and 1.8 in the air. I was pleased to still know what to do.
So I reserved a plane for Saturday to fly to Scappoose. Then this morning the weather was marginal and so was my health. I decided to stay on the ground today.
So I reserved a plane for Saturday to fly to Scappoose. Then this morning the weather was marginal and so was my health. I decided to stay on the ground today.
Sunday, June 6, 2010
Wrapping up the Roll bar
We've gotten the roll bar all riveted together, and now we are working on the custom fit with the brackets. Here are a few shots of the process.

First we started by clamping the parts to a rigid board. Then we secured the parts to the board with clamps and clecoes. We tried to be very careful with the width and the height. Also we measured the mid-point as a control.

We measured carefully to space the holes properly. Nobody is better at careful measurement than Bob.

Then we riveted the F-631 plate to the channels. We chose to pop rivet the assembly to the board so it wouldn't move while we were working on it.

We used a clamp to hold the pieces in the proper place.
After we got the back side all drilled, we determined that the flanges of the channels were not at a 90 degree angle. The reason we were concerned is because there was a gap between the flange and the strap. So we tried to fix that by bending with a spanner wrench. This proved to be effective but a little tedious.
There were many iterations of adjusting, checking and marking. Then do it again. Finally the fit was darn near perfect. One concern was the marks left in the radius of the bend by the spanner wrench. We were able for the most part to scotch brite out these marks.

When it came time to drill the front side channels, we made a tool to keep a 1.5" total thickness. For the most part it worked well, but we found that when it was all riveted together the bottom of the bow was 1/10" wider than expected on both ends (1.6"). There isn't much that can be done at this point, but we decided it will be okay.

We press on. Now we are working on the attachments to the fuselage. As you know they are a custom fit.

First we started by clamping the parts to a rigid board. Then we secured the parts to the board with clamps and clecoes. We tried to be very careful with the width and the height. Also we measured the mid-point as a control.

We measured carefully to space the holes properly. Nobody is better at careful measurement than Bob.

Then we riveted the F-631 plate to the channels. We chose to pop rivet the assembly to the board so it wouldn't move while we were working on it.

We used a clamp to hold the pieces in the proper place.
After we got the back side all drilled, we determined that the flanges of the channels were not at a 90 degree angle. The reason we were concerned is because there was a gap between the flange and the strap. So we tried to fix that by bending with a spanner wrench. This proved to be effective but a little tedious.

There were many iterations of adjusting, checking and marking. Then do it again. Finally the fit was darn near perfect. One concern was the marks left in the radius of the bend by the spanner wrench. We were able for the most part to scotch brite out these marks.

When it came time to drill the front side channels, we made a tool to keep a 1.5" total thickness. For the most part it worked well, but we found that when it was all riveted together the bottom of the bow was 1/10" wider than expected on both ends (1.6"). There isn't much that can be done at this point, but we decided it will be okay.

We press on. Now we are working on the attachments to the fuselage. As you know they are a custom fit.
Wednesday, May 12, 2010
Starting on the roll bar
Bob got back from three weeks of traveling last night. Master Chief is still missing in action (on a cruise).
Tonight I worked at my tube bending technique. Still needs work.
The 21' of new tubing and the screws I ordered have arrived. I am not too sure about the tiny little allen heads. I'm afraid I may break an allen wrench if I have to torque on these to get them set.

I bought a plastic covered piece of shelving material for laying up our roll bar. The board is really stiff. I think it will work well. I was glad that Bob and I were working together; instead of 'close enough' We came close to breaking out the micrometer.
Here's a picture of the tunnel mod we finally settled on. It's a little embarrassing to think how much time was spent doing this. The benefit will come if we ever need to access where the fuel line come out of the tunnel.

As you may know, I've been kind of consumed with the idea of rolling my own lights with LED's. So while I was at Sun n' Fun a few weeks ago, I snapped a couple pictures of interesting applications. I'm still fussing over how I want to do ours.
Tonight I worked at my tube bending technique. Still needs work.
The 21' of new tubing and the screws I ordered have arrived. I am not too sure about the tiny little allen heads. I'm afraid I may break an allen wrench if I have to torque on these to get them set.
I bought a plastic covered piece of shelving material for laying up our roll bar. The board is really stiff. I think it will work well. I was glad that Bob and I were working together; instead of 'close enough' We came close to breaking out the micrometer.
Here's a picture of the tunnel mod we finally settled on. It's a little embarrassing to think how much time was spent doing this. The benefit will come if we ever need to access where the fuel line come out of the tunnel.
As you may know, I've been kind of consumed with the idea of rolling my own lights with LED's. So while I was at Sun n' Fun a few weeks ago, I snapped a couple pictures of interesting applications. I'm still fussing over how I want to do ours.
Tuesday, March 2, 2010
We continue to work
Most recently Bob has been working on the center section between the fuel selector and the firewall. He has devised a plan to modify the access panel below the cabin heat distributor box. He is working on the finer points of that.
Last night I was working on the rudder pedals; installing the cotter pins in the castle nuts. Also, getting the brake lines ready for installation. I still wrestle with the idea of spending more money for better brake lines, but see lots of big ticket items still looming on the horizon.
I've been researching LED's and how to design the wingtip lighting.
Also, I've been reading up on the roll bar and how it goes together. I need to come up with a board that will be suitable to clamp the roll bar down and keep it straight.
We are often anxious to make better progress, but take solace in the knowledge that this is not a race. It is a hobby, and we are constantly learning new skills in the process of building. We can't help but be eager to 'gitter done'.
Last night I was working on the rudder pedals; installing the cotter pins in the castle nuts. Also, getting the brake lines ready for installation. I still wrestle with the idea of spending more money for better brake lines, but see lots of big ticket items still looming on the horizon.
I've been researching LED's and how to design the wingtip lighting.
Also, I've been reading up on the roll bar and how it goes together. I need to come up with a board that will be suitable to clamp the roll bar down and keep it straight.
We are often anxious to make better progress, but take solace in the knowledge that this is not a race. It is a hobby, and we are constantly learning new skills in the process of building. We can't help but be eager to 'gitter done'.
Thursday, February 11, 2010
Heater
Bob is working on the pieces that will become our cabin heater. It will also, be the cover for our fuel lines.
A welding we will go...
After the presentation, those that wanted could try their hand at striking an arc.
For myself, I found the information interesting, but I'm happy that I have friends who can weld.
Labels:
Welding
Subscribe to:
Posts (Atom)
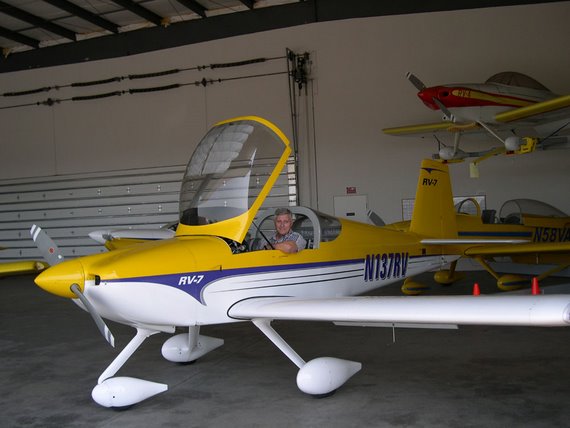
Before we decided to build an RV9A we were looking at the RV7A. This picture was taken on a factory tour.
Standard (aka Slow build) RV9a kit
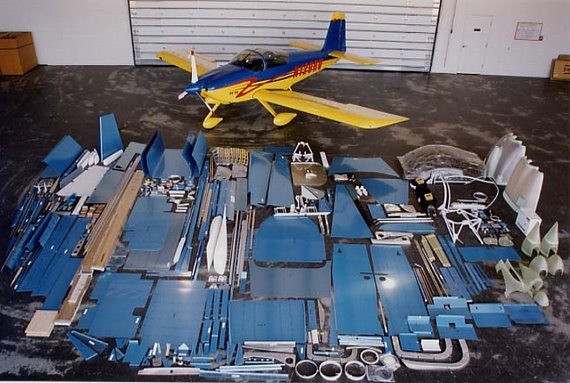
Quick build RV7 kit
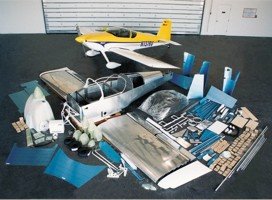
The Process
Most of us think of the airframe as the main thing, and I suppose it is; since you can't fly without it. The kits that Vans sells are match hole punched. That means that the holes are already located and punched when you get them. This saves a lot of time as you can imagine. So what follows is what you do once you've unpacked and inventoried the parts from the factory.
There are several thousands of these planes flying. Rather than making mistakes first-hand, I recommend looking at the web sites of builders who have already done this. Some of my favorite links are provided. You should also look at Van's 'Links' page for the model you're building.
Before touching the parts, it is advisable to read the instructions and review the drawings until you have a clear idea what needs to happen and what sequence it needs to happen in. The drawings are invaluable.
Each sub assembly requires the same basic process:
1. Prepare the parts for fitting. This entails cleaning, filing, and finally scotchbrighting. In addition, some parts require fabrication and/or machining.
2. Fitting is done numerous times. The pre-punched holes are matched to the corresponding part(s) and are held together with clecos.
3. Match drilling is done in assembly to provide optimum fit.
4. Once the holes are match drilled to the proper sizes, the part is disassembled and deburred to remove any sharp edges and irregularities that might result in a poor fit or the development of a crack.
5. Rivets that will be flush with the skin require either a dimple or countersinking. This is normally obvious, but sometimes the rivet needs to be flush and it's not clear at first glance just why.
6. At this point, a coat of primer and (in some cases) paint is applied protect the metal from corrosion. We've decided to prime and paint all skeletal parts; i.e. Spars, Ribs, etc. Skins will be primed where they connect. The method to our madness is this; we want defects to appear first in the skin where they are easiest to fix and pose less of a threat.
7. This is a dangerous part of the process because you might want to rivet something. But WAIT! Review the plans and the directions again.
8. Okay, so you've reviewed the plans and the parts are ready to assemble. Double and triple check the plans to ensure that the proper rivets are used. It's easy to mess this up or get out of sequence.
There are several thousands of these planes flying. Rather than making mistakes first-hand, I recommend looking at the web sites of builders who have already done this. Some of my favorite links are provided. You should also look at Van's 'Links' page for the model you're building.
Before touching the parts, it is advisable to read the instructions and review the drawings until you have a clear idea what needs to happen and what sequence it needs to happen in. The drawings are invaluable.
Each sub assembly requires the same basic process:
1. Prepare the parts for fitting. This entails cleaning, filing, and finally scotchbrighting. In addition, some parts require fabrication and/or machining.
2. Fitting is done numerous times. The pre-punched holes are matched to the corresponding part(s) and are held together with clecos.
3. Match drilling is done in assembly to provide optimum fit.
4. Once the holes are match drilled to the proper sizes, the part is disassembled and deburred to remove any sharp edges and irregularities that might result in a poor fit or the development of a crack.
5. Rivets that will be flush with the skin require either a dimple or countersinking. This is normally obvious, but sometimes the rivet needs to be flush and it's not clear at first glance just why.
6. At this point, a coat of primer and (in some cases) paint is applied protect the metal from corrosion. We've decided to prime and paint all skeletal parts; i.e. Spars, Ribs, etc. Skins will be primed where they connect. The method to our madness is this; we want defects to appear first in the skin where they are easiest to fix and pose less of a threat.
7. This is a dangerous part of the process because you might want to rivet something. But WAIT! Review the plans and the directions again.
8. Okay, so you've reviewed the plans and the parts are ready to assemble. Double and triple check the plans to ensure that the proper rivets are used. It's easy to mess this up or get out of sequence.
Rivets and Riveting
There are thousands of rivets that hold the plane together. Since this is an important task, let's talk a bit about them.
The rivets we'll be using are made of aluminium and are set in one of several ways; Hammering, Squeezing, Pull through.
Hammering a rivet is best done with a partner. One person operates the rivet gun and the other holds a bucking bar on the back side to create a shop head. I've tried doing this alone and almost always with undesirable results. The idea is for the shop head to be approx 1.5 times the diameter of the shank of the rivet.
Squeezing a rivet requires a special tool and is my preferred way whenever possible. Some folks use a manual squeezer, but I like pneumatic squeezer. They develop approx 3,000 pounds of force in the last 1/8th inch of the piston's travel. So proper adjustment is important. Once adjusted properly it will deliver consistent rivet sets.
Pull through (aka Blind or Pop) rivets are for those applications where there is no way to get access to the back side of the rivet. In general this type of rivet has inferior strength characteristics compared to a solid rivet. The noteworthy exception is the Cherry Max rivet. It is a pull through rivet, but it is also structurally rated and not cheap.
The rivets we'll be using are made of aluminium and are set in one of several ways; Hammering, Squeezing, Pull through.
Hammering a rivet is best done with a partner. One person operates the rivet gun and the other holds a bucking bar on the back side to create a shop head. I've tried doing this alone and almost always with undesirable results. The idea is for the shop head to be approx 1.5 times the diameter of the shank of the rivet.
Squeezing a rivet requires a special tool and is my preferred way whenever possible. Some folks use a manual squeezer, but I like pneumatic squeezer. They develop approx 3,000 pounds of force in the last 1/8th inch of the piston's travel. So proper adjustment is important. Once adjusted properly it will deliver consistent rivet sets.
Pull through (aka Blind or Pop) rivets are for those applications where there is no way to get access to the back side of the rivet. In general this type of rivet has inferior strength characteristics compared to a solid rivet. The noteworthy exception is the Cherry Max rivet. It is a pull through rivet, but it is also structurally rated and not cheap.
Removal
When rivets are set badly (as is sometimes the case) You need to decide if it's so bad that it just has to be replaced or is it okay as is. The main concern is to remove the offending rivet without doing damage to the hole it's in; e.g. enlarging or elongating or both.
When rivets are set badly (as is sometimes the case) You need to decide if it's so bad that it just has to be replaced or is it okay as is. The main concern is to remove the offending rivet without doing damage to the hole it's in; e.g. enlarging or elongating or both.
If it just doesn't pass muster, get a drill bit about the diameter of the rivet shaft or smaller. Center punch the head of the rivet (solid rivets only) and then carefully drill thru the head just down to where the shaft meets the hole. Once this is done, insert and old drill bit into the hole and wiggle the head until it snaps off. Once the head is off you should be able to push it out with a punch.
With pull through rivets this can be problematic, as the shaft is most likely steel and may turn with the drill bit. Another problem with removing blind rivets is this. Blind rivets are used because access to the back side is either difficult or impossible. Onc you commit to removing the blind rivet, you have to figure out how to remove the back side when you punch it thru the hole.